After-sale support is an integral part of MBF’s philosophy. From the original concept of a MBF product, our loyalty to our customers and to the equipment is of crucial importance. Our dedicated After-Sales Department displays a passion to ensure efficienty and longevity from your investment.
Customer support and service is paramount at every step throughout the process, even after the sale is complete.
The Assistance Service is divided into two sections: preventive and corrective.
In the first case, a systematic monitoring of the machines, configurations, and complete lines at a customer site is performed.
In the second case, the service is carried out by technical personnel of sales representatives and local distributors who receive further training on a day-to-day basis; however, in more complex cases, personnel from the parent company are directly involved.
The scheduled periodic reviews help keep the machinery in perfect condition and ensure customers maximum and constant efficiency.
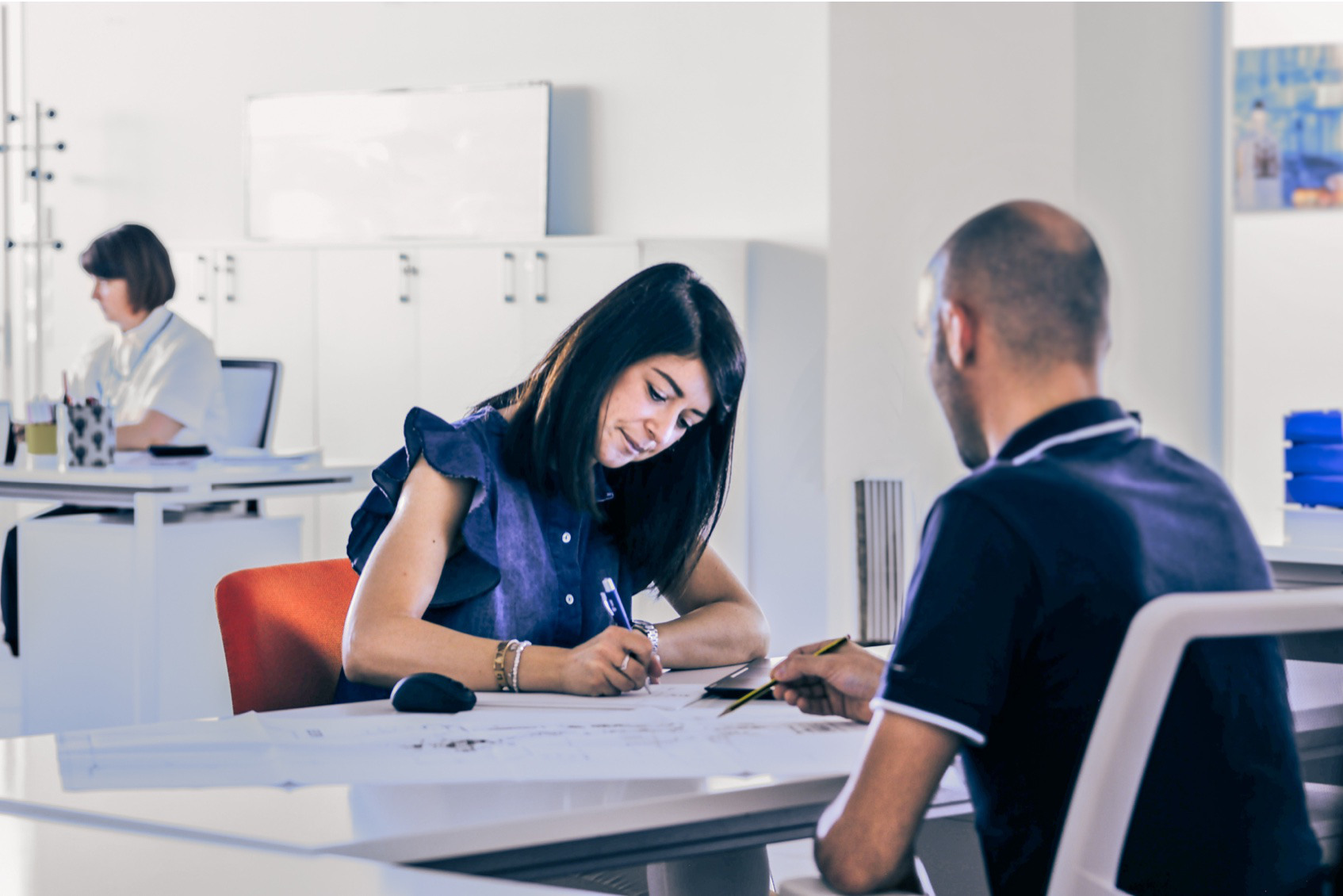
Discuss with our Technical Experts and find the best solution for your bottling line, or new piece of equipment to be integrated in an existing line. We can survey your existing equipment, discuss your needs and work together to design the optimal solution for your needs and for your budget
MBF handles the entire project management experience, from start to finish. This includes design and installation of the bottling line, with an eye on the entire production area to ensure the highest quality standard. Each project is assigned to a Project Manager who follows the job order from start to finish, assuming the role of contact point between the customer and all those involved at the company.
MBF takes the entire production process into consideration, including the arrival of empty bottles into the bottling area, to all stages of filling, capping, and labeling, to packing and shipping of the final product.
The project management is a large advantage to customers, offering a dedicated partner that will act in a timely manner on all issues involved with the bottling line.
Supply and installation of quality packaging and automation equipment.
From single machine to full turn-key packaging lines, MBF North America can supply and install a complete range of packaging and automation equipment at your site.
- De-palletisers, Palletisers
- Rinsers
- Fillers
- Cappers and Corkers
- Hooders and Wirers (muselet)
- Labellers
- Carton erector and sealers
- Case and wrap-around packers
- Shrink-wrappers (including tray+film)
- Pallet wrappers
- Quality control and inspection systems
- Conveyor systems
Our qualified team of technicians are available to provide a range of services to our entire equipment portfolio. MBF North America is self-sufficient in all mechanical and electrical works and can assist with production support, breakdowns and regular servicing and maintenance of all types of equipment.
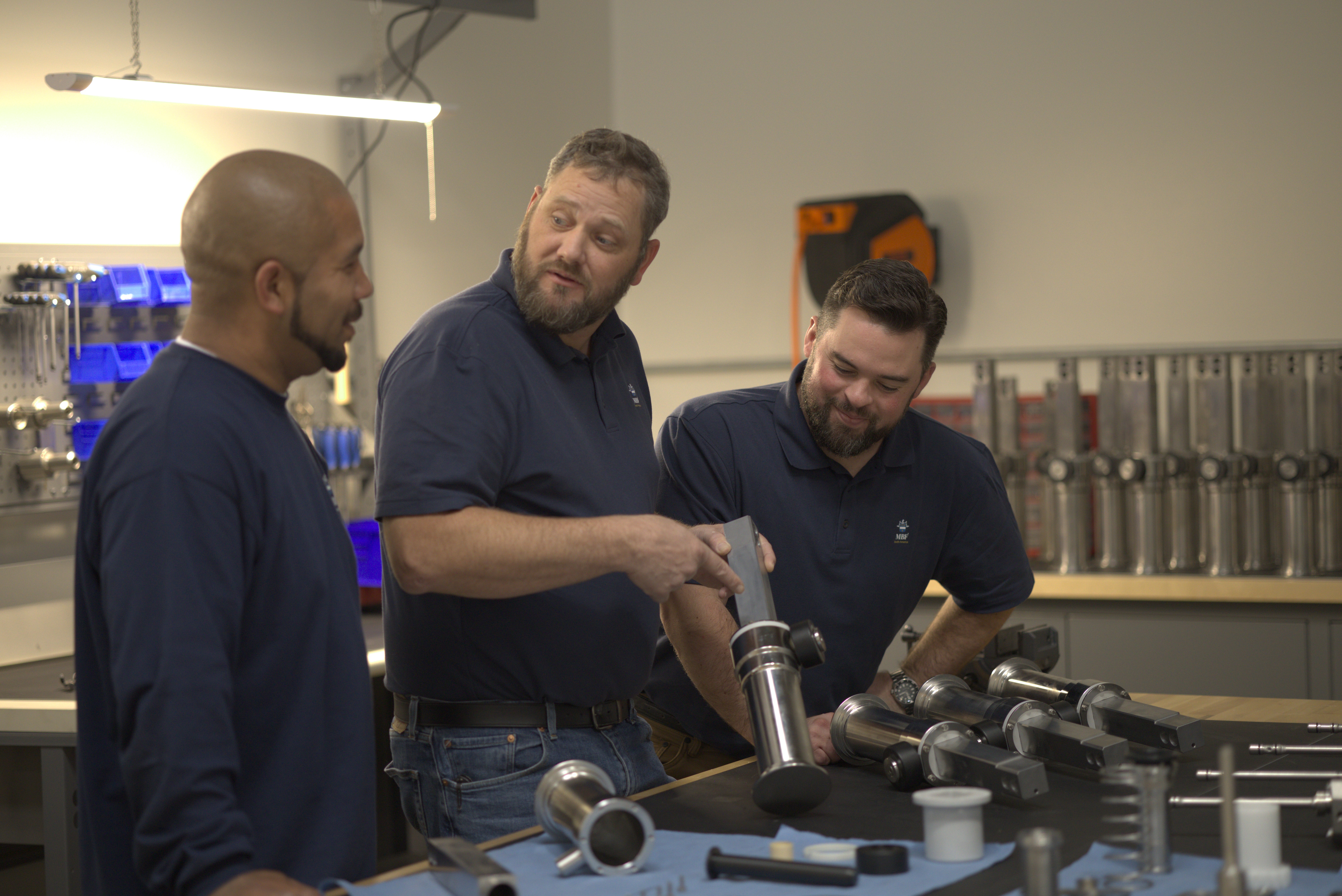
Quickly replace your repetitive parts like a filling valve, a cleaner gripper and ship them to our Remote Maintenance Workshop, where a team of specialized technicians will laser- mark, inspect, disassemble, thoroughly clean, repair/replace what’s needed and rebuild your parts, that will then be shipped with a detailed health status. Contact our Service Dept to get to know the advantages of this innovative service that minimize your downtimes and maintenance costs, while increasing your equipment’s reliability and quality performance.
Minimize your Total Cost of Ownership with the support of our Parts Specialists who will propose the best strategy for your inventory of parts in conjunction with our stock. Choose one of our Preventive Maintenance Plans and let’s work together to keep your machines up and running.
We hold an extensive inventory of stock for each of our represented suppliers, giving you the confidence and reliability to minimize down-time within the production environment.
Training, with both customers and distributors, is an equally important aspect of the company.
Education and machinery knowledge is shared in order to benefit everyone involved and maximize a machine’s performance.
MBF provides certified training courses at various levels, to the sales force and technicians of the headquarters, distributors and customers.
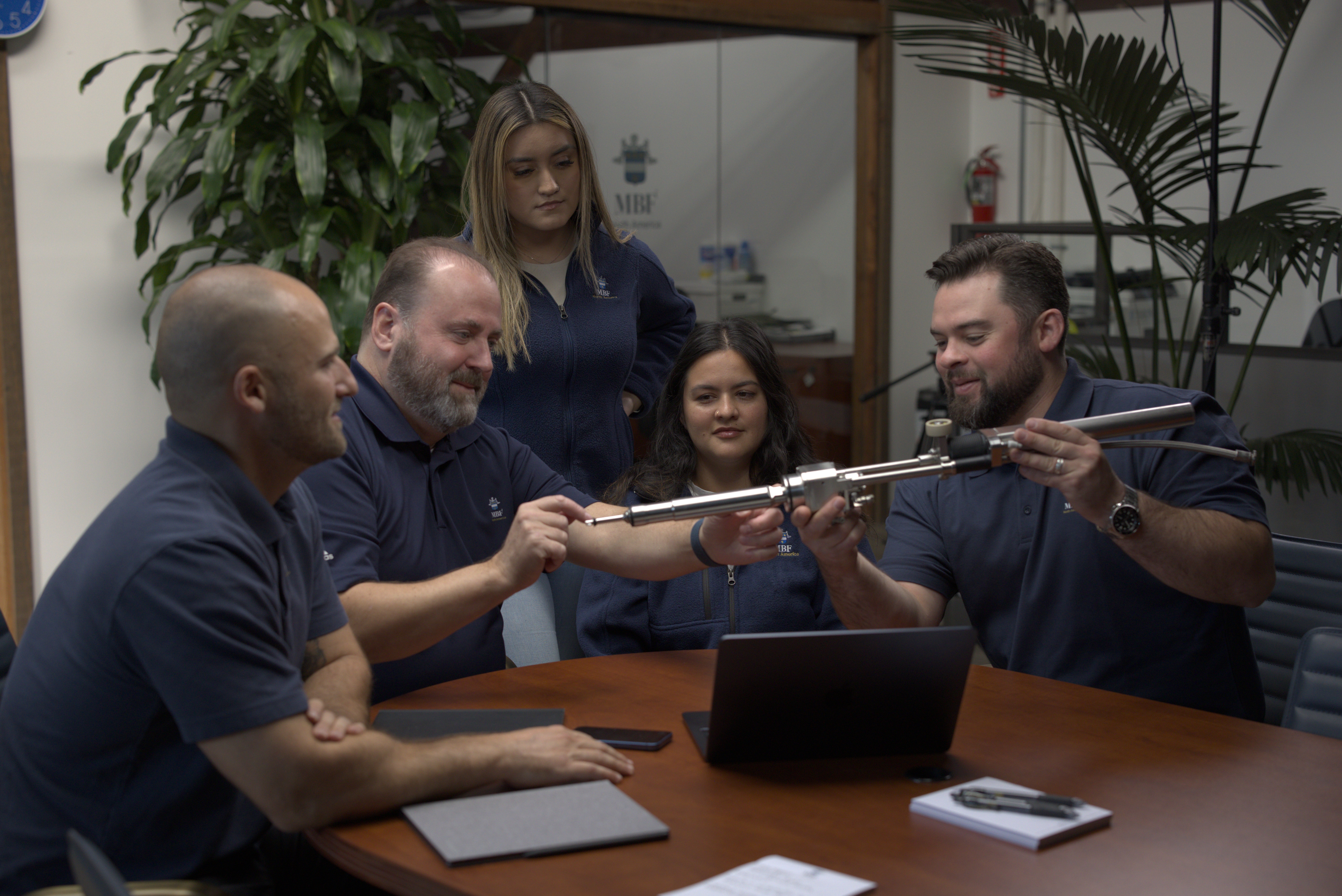
For a fast answer to all our customers needs, we have established 3 different service centers to store our spare parts.
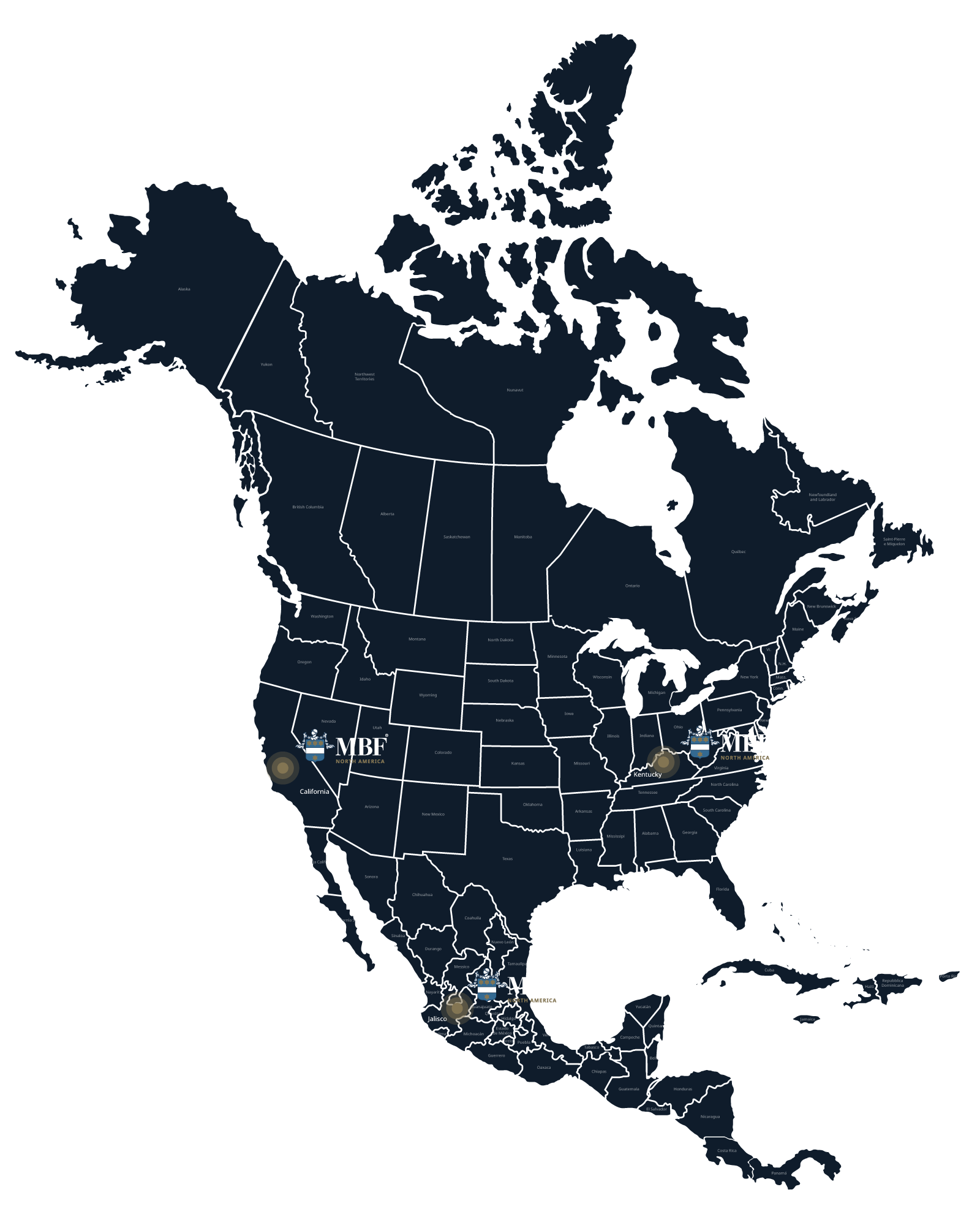
California
429 First Street, Suite 120/220
Petaluma, CA 94952
Kentucky
2129 Commercial Drive, Suite A
Frankfort, KY 40601
Mexico
Av. Cristóbal Colón #4351
Col. Nueva España
Guadalajara, Jalisco. CP.44980